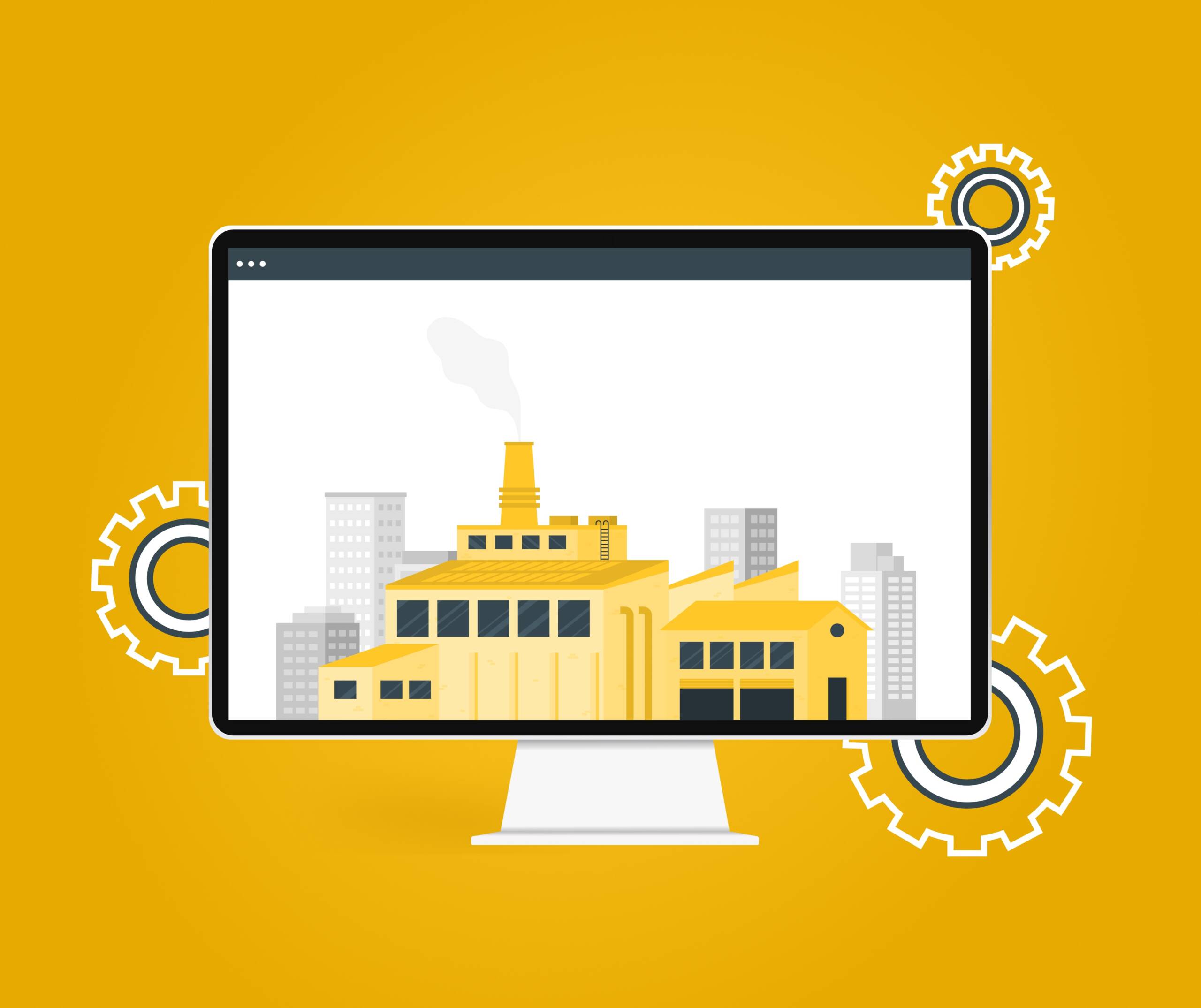
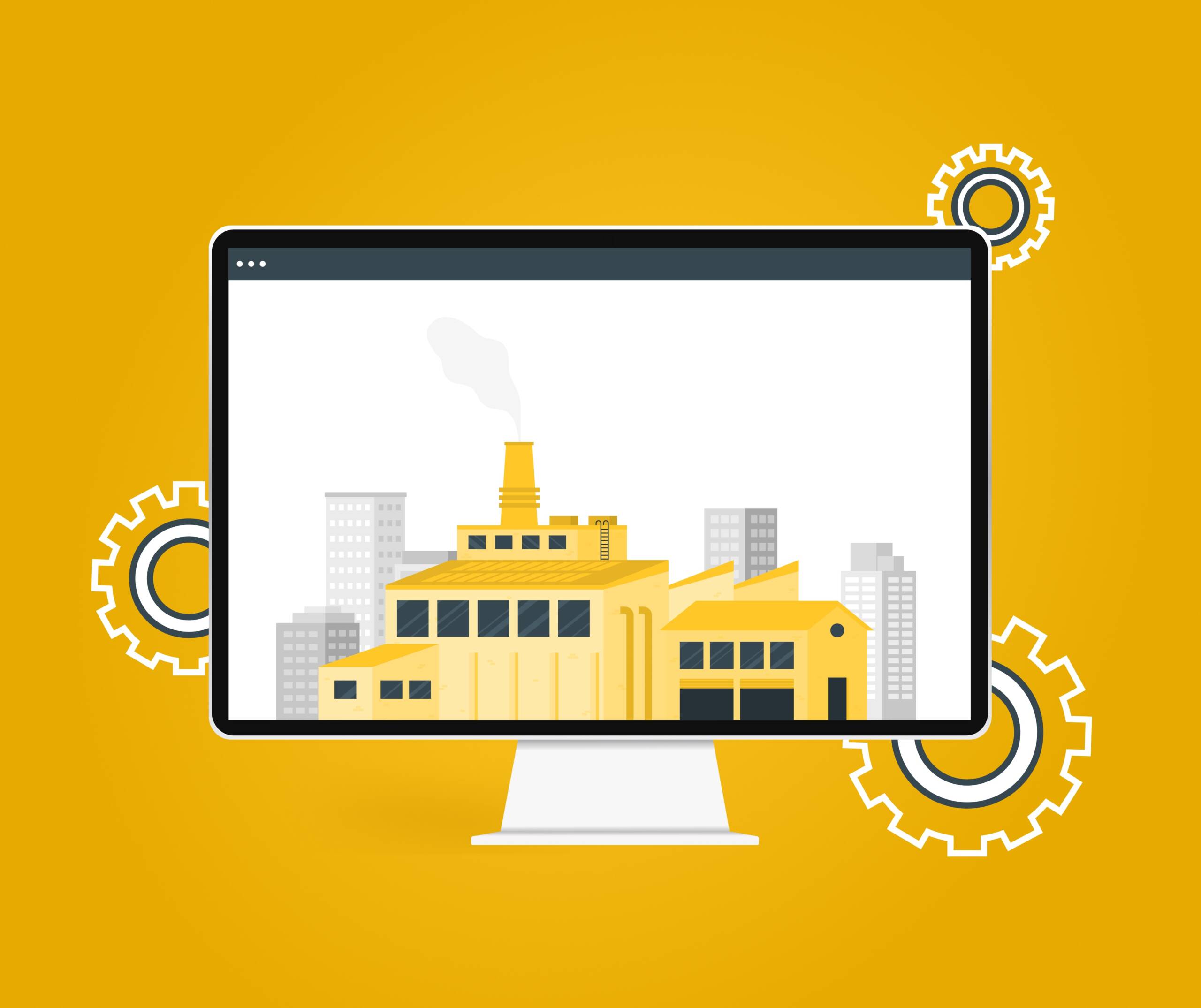
How Digital is Transforming the Industrial Supply Chain
The recent pandemic has amplified the structural vulnerability of the global industrial supply chain, with shortages of everything from basic grocery items to industrial machining components. During the COVID-19 crisis, the most challenging needs were largely met by stretching the power and reach of the internet to connect end buyers with manufacturers.
Digital transformation of our lifestyles has extended beyond working from home or online education into the areas of our business and industrial activities as well. The industrial supply chain was no exception, incorporating and adapting to various digital and analytical solutions that typify “Industry 4.0” by helping balance productivity with supply and demand.
The industrial supply chain in the digital age is benefiting from the opportunities created by smart and integrated digital strategies that connect all aspects of the business, from OEMs (Original Equipment Manufacturers) to Tier 1, 2, and 3 suppliers, to streamline operations, drive profitability, and enable growth.
Understanding OEMs vs. Tier 1, 2, and 3 Suppliers
To understand the digital impact on the industrial supply chain, let’s first understand the various stages involved in the process.
It’s a known fact that few companies produce, distribute, and sell products end-to-end all by themselves. The famous video of Milton Friedman detailing all of the suppliers involved in pencil production is an example of the significance of Tier 1, 2, and 3 suppliers and how they differ from Original Equipment Manufacturers (OEMs).
Statistics show us that an automobile manufacturer has around 250 tier-one suppliers on average, and amazingly the number often reaches up to 18,000 across the full value chain. Similarly, aerospace manufacturers have an average of 200 tier-one suppliers and 12,000 across all tiers. Similarly, technology companies have an average of 125 suppliers in their tier-one group and more than 7,000 suppliers across all tiers.
So what do the different terms “mean,” and how are they used to categorize the components of an industrial value chain?
OEMs (Original Equipment Manufacturers)
Perhaps the best example for helping anyone understand the relationship of OEMs to suppliers is the automotive industry. It might surprise some people to know that an average car consists of roughly 30,000 parts. Automotive OEMs like Ford, Toyota, and others are not so much “manufacturers” as they are designers and integrators of these many components to create the final product (the finished and driveable cars), while the components themselves are sourced from suppliers that are typically designated as Tier 1, 2, or 3.
What are Tier 1 Suppliers?
Companies that supply parts or materials directly to OEMs are called Tier 1 suppliers. They are the largest supplier of the trio. Such suppliers typically have an exclusive relationship with a few OEMs in a specific market. For example, a company selling branded apparel is an OEM: The factory assembling the company’s cotton t-shirts is a Tier 1 supplier.
Tier 2 Suppliers
Tier 2 suppliers are smaller in general and have fewer production and workforce resources in comparison to Tier 1 companies. These firms supply parts or materials that wind up in the end product, even though they do not sell directly to the OEMs. The t-shirt factory, according to the earlier example, receives its materials from a fabric mill. This fabric mill is considered a Tier 2 supplier to the apparel company.
Tier 3 Suppliers
Generally, OEMs, Tier 1, and Tier 2 companies need various kinds of raw materials. Tier 3 refers to suppliers of raw materials or close to raw materials like metal or plastic. Tier 3 companies supply to all levels. As per the above example, the Tier 3 supplier is the farm that sells cotton to the fabric mill at Tier 2.
Tier N Suppliers
Finally, Tier N works as a sub-tier in the various base levels of the supply chain. However, they are not always identified in the chain. So they tend to increase the risk to the higher tiers if any disruption happens in the supply chain process. This was evident in the recent pandemic. The farm that grows the cotton has its Tier N supplying the cotton seeds, fertilizers, and other agricultural materials.
Digital Transformation of the Industrial Supply Chain
The term “digital transformation” often refers to the use of digital technologies to reinvent the way a company does business, typically to make the business more productive, agile, and responsive to deliver higher value to customers at lower costs.
Perhaps nowhere has the power of digital transformation been so evident as within industrial manufacturing ecosystems. Here are a few examples and areas of the industrial supply chain that are benefitting from the latest developments in digitization:
R&D and Product Design
Digital enables research and development through innovations such as simulation-based designs and “digital twins,” or digital copies of an actual physical product, process, or ecosystem that can be used to run virtual simulations. Data from the real world is used to update and change the digital twin to reflect any changes in the actual operating environment. This digital twin can be used in R&D to test different simulations or designs before investing in a solid prototype design.
Connected hardware produces more robust data for companies to analyze and incorporate with portfolio analytics for more informed and effective project/production prioritization. Put simply, digitization enables industrial businesses to match the right projects with the right resources. This mostly benefits OEMs. However, Tier 1 and Tier 2 suppliers are also leveraging R&D to improve their own production systems in similar ways so they can more effectively support OEMs.
Procurement
The pandemic has proven that procurement functions can deliver quickly when adapting to the digital landscape. Digital innovation in procurement is moving beyond traditional sourcing strategies and research for negotiating pricing. It is now enabling a more insightful gathering through newer norms of spend analytics.
Applying spend analytics to the procurement function can help a manufacturing organization find a better balance between cost and speed, and use the resulting understanding to make better decisions and ensure that they’re spending wisely. The spend analytics helps the manufacturers and the suppliers in two important ways.
- Helpful for OEMs to see how suppliers are affecting their profitability.
- Helps the suppliers they can create efficiencies that allow them to offer supply at more competitive costs.
Digital procurement is further enabled by e-platforms designed specifically for managing vendor auctions. This mostly applies to Tier 1 raw materials suppliers since they typically source commodities with highly fluctuating prices influenced by continuously changing market dynamics. This includes, for example, digital verifications that improve cost efficiencies at all stages of the supply chain that are subject to strict regulatory oversights.
Manufacturing and Production
The application of information and communication technology (ICT) to every facet of manufacturing is revolutionizing all industrial market sectors, in fact, changing how products are designed, fabricated, used, operated, and serviced post-sale. It is also transforming processes, operations, the energy footprint of factories, and the management of industrial supply chains.
The digital transformation of manufacturing industries is popularly referred to as “Industry 4.0” in Europe, or the “Industrial Internet of Things (IIoT), in the US, or just “smart manufacturing” in general. Specifically, this digital transformation is advancing the manufacturing process in ways such as:
- Internet-connected machines generate data that support predictive maintenance and quality assurance. This mostly supports all three Tiers of suppliers. However, some OEMs will also have advanced and proprietary systems for finishing the final product.
- Automated robotic welding and assembly of parts are changing the business model for many Tier 1 and Tier 2 suppliers in markets such as the automotive and precision manufacturing industries. Some OEMs are also using robotics for final product assembly.
- Inventory management and production systems integrated with AI and machine learning are helping manufacturers increase efficiencies throughout the value chain to the benefit of both OEMs and the suppliers they do business with.
- Additive manufacturing (3D printing) has reduced cost-per-part across manufacturing verticals by 60% since 1990.
- Smart plants enabled by digitization and automation achieve more cost-efficient mass production, while customer-centric plants are using digital to offer ultra-responsive mass customization at scale.
Warehouse and Logistics
Traditionally, warehouse and logistics have focused on lean warehousing and inventory management to support business-friendly vendor sales and operations. Now digital technologies driven by AI-supported predictive analytical models are enabling footprint optimization, along with more intelligent routing and sourcing.
This not only helps the end manufacturer maximize their profitability but also helps vendors and suppliers operate with more confidence and efficiency when they know sooner and in more detail what their end buyers need, how much they need, and when they will need it delivered.
How Industrial Companies Can Benefit
Ultimately, digital technology enables businesses operating at every stage of the industrial supply chain to better prepare for future challenges, including unprecedented events such as the pandemic, while also building operational resiliency and maintaining–or in many cases, increasing–their production efficiencies.
A digital partner like DBS that understands all the complexities of manufacturing, including custom development of web technologies and software applications, can help you achieve your goals for digital transformation, whether you’re a tiered supplier or an OEM.
Contact us to learn more about your opportunities and how we can help you capitalize on them through digital strategy and development.
FAQs
Tier 1 companies supply materials to the OEM (original equipment manufacturer). Tier 2 supplies to Tier 1, and Tier 3 supplies to Tier 2. At the very bottom of the supply chain is Tier N which collectively supplies basic raw materials to Tier 3.
Following are the areas of the industrial supply chain that digital transformation has been most effective:
R&D and Product Design
Procurement
Manufacturing and Production
Warehouse and Logistics
Digital transformation of the industrial supply chain refers to using digital technologies to reinvent the way a manufacturer does business. This is typically adapted to make the business more productive, agile, and responsive, thereby delivering higher value to customers at a lower cost.